Maintenance of vulcanizing presses
Follow the recommended preventive maintenance schedule provided with the press
Each press, depending on its type and capabilities, requires individual maintenance. We recommend in first instance to follow the maintenance schedule comprised in the manual of a given machine, even though most hydraulic presses have similar maintenance needs.
Check oil level and operating temperature
Improper oil level may lead to a pump failure due to cavitation phenomenon in which air enters the pumped medium, while too warm oil may cause premature failure of the pump. In addition, monitoring of oil temperature allows detection of abnormalities in the circuit components. Sudden heating up of any system of a press, which usually runs at a low temperature, may indicate a faulty element through which oil enters and causes system overheating.
Make sure oil is clean
Contaminated oil may cause considerable damage of the components, unplanned downtime and overall system failure. Basic hydraulic systems often operate with simple, coarse 10-micron filters in return lines, while higher capacity systems, which use proportional valves or servo valves require finer filtration (6-micron filters) in combination with built-in pressure and return filters. The manufacturer should specify the type of system and the required cleanness grade. Periodical taking and analysing oil samples by a third-party contractor or an authorized oil testing lab is recommended. Often, a local distributor of hydraulic components may do it or suggest a reliable contractor to perform these services.
Pay attention to joining parts
Any press, irrespective of its frame structure: either fully welded or made with use of tie rods, contains numerous threaded connections, and proper quality of bolts and nuts is a pre-condition of its proper operation. Check actuator fastening monthly and make sure all bolts are tightened to the correct torque. Use baseline markings as quick reference indicators for future monitoring. Many presses have markings on the mounting bolts to confirm they have been tightened to the correct torque. Also monitor joining parts of a table top and nuts to tighten tie rods.
Monitor safety system daily
Prior to start up the press, check all safety systems including light curtains, safety doors, safety mats, etc. Upon detecting any faulty or unreliable safety device, stop immediately and lock the press and call the service people. Check operation of emergency stop circuit daily.
Record press data
The best tool to monitor performance of press system is data logging, although it is not often used. Data acquired such as evolution of operating pressure during press cycle, high-speed in-feed and compacting, and high-speed retracting may provide important information on the performance of press systems. The press manufacturer should record these data during the equipment testing and made them available to the user. The best opportunity to record this data is at the press start-up. Data acquired should be reviewed periodically. Any occurred increase of operating pressure means the components work under their optimum performances and may have failed.
Pro-actively replace wearing parts of a press
The vast majority of presses is made of several hydraulic components manufactured by the same or various manufacturers. Each manufacturer informs about the expected service life of each component. Pro-active replacement of a component before it has failed prevents unexpected downtime and expensive repairs. Hydraulic components (pumps, in particular) may fail and contaminate hydraulic system, therefore regular replacement of their components is much easier and much cheaper solution than waiting until the component has failed and possibly contaminated the system.
Any problems? Just come to us! We’ll find the right solution for you! Let’s find out together how to increase effectively and cost-efficiently your production performances. Contact us and let’s talk about available options.
Let’s keep in touch
At KONEK PSN, we take on challenges related to servicing vulcanizing presses. If you have any questions or special request – just call us: +48 52 379 26 53 or write to our e-mail address: info@konek.com.pl.
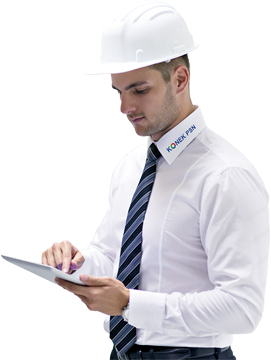